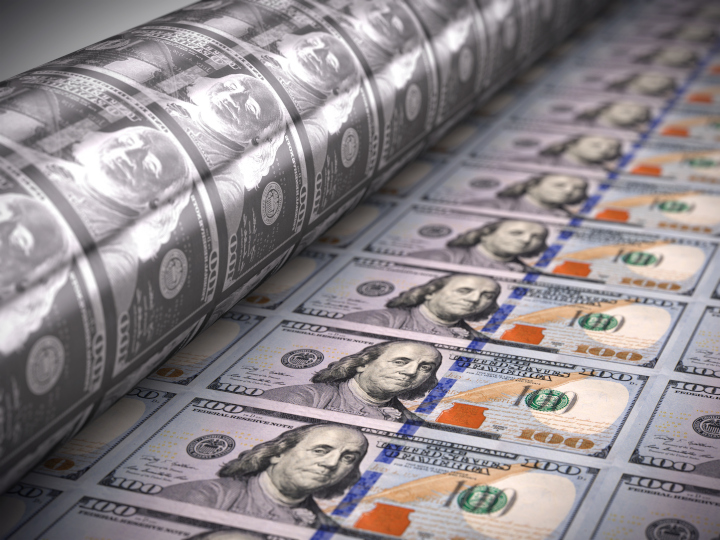
Photo purchased from … www.depositphotos.com
While it’s still considered legal tender, open your wallet and look closely at some of the paper money, the bills, of various denominations. How are they printed, where are they printed, and by whom are they printed?
Where And By Whom?
The easiest answers are where and by whom. All paper bills are printed by the US Bureau of Engraving and Printing, which has one plant in Washington, DC, and one plant in Fort Worth, Texas. The Bureau of Engraving and Printing also designs all the various denominations and checks all the printed bills for accuracy before trimming and wrapping them.
But How Are They Printed?
Let’s start with the paper substrate. Currency paper is composed of 75 percent cotton fibers and 25 percent linen fibers. After all, bills have to tolerate heavy use over a long period of time, and this stock is very durable. It is also highly controlled and tracked (each and every sheet) to prevent theft by counterfeiters. In addition, the paper is laced with various colored threads, called “security threads” (some of which glow under UV light) to distinguish the stock from non-currency paper, again to minimize counterfeiting.
Now, the inks. For the graphics (text, numerals, and image on the back, and portrait, text, serial numbers, and such, on the front), custom printing inks include green for the back (primarily, although I see a little yellow as well on my $20), as well as black, green, metallic, and color-shifting ink (which changes color depending on the viewing angle) for the front of the bills. These are proprietary inks developed by the Bureau of Engraving and Printing.
In addition to being used for the numerals, text, and portraits, the inks are used for various security features such as micro printing, and the paper contains watermarks of various kinds (portrait and numeric). There’s even a 3D strip woven into the new $100 bills to prevent counterfeiting.
Now for the commercial printing technology. I had initially expected the bills to have been printed via gravure technology (a direct-printing technology using etched custom printing cylinders with little wells to collect and transfer the ink). Why? Because it’s supremely economical for exceptionally long press runs.
So I was surprised to discover in my research that gravure is not used. Instead the bills of all denominations are printed via both offset lithography and dry intaglio custom printing.
The offset printing component is done first, with the background green color being applied to both the back and the front of the bills, with 72 hours’ of drying time in each case before the following step.
Each printed sheet contains 32 notes, side by side, before they are cut down into individual bills. But this was not always the case. Initially the bills were larger, and were printed eight-up (eight rather than 32 bills on a press sheet). Changing the ink formulation over the years (plus changing the chemistry to eliminate water from the mix) allowed for faster drying and the inclusion of more bills on each press sheet.
After the offset printing step (which prints from metal plates first onto rubber press blankets and from these press blankets onto the custom printing paper), the next step is the dry intaglio printing (the engraving).
Intaglio plates have recessed image areas. (This is in contrast to offset plates, on which image areas and non-image areas are on the same flat plate. This process works due to the inability of ink and water to mix. Image areas are treated to attract ink and repel water; non-image areas are treated to repel ink and attract water.)
The intaglio printing process is used specifically for the fine detail work on both sides of the currency. This includes the portraits, some of the numerals, scrollwork, etc. First the plates are inked up, allowing ink to seep into the recesses of the etched plates (artwork is designed separately and then etched into the plates with sharp tools and acids in a process called “siderography”). Then the ink is wiped off the surface of the plates (although ink that has seeped into the recesses of the plates stays in these etched image areas). Finally, the intense pressure of the intaglio rotary press actually forces the paper into the etched areas, making the paper absorb ink and also rise up slightly above the otherwise flat surface of the custom printing stock.
The dry intaglio process prints the backs of the press sheets first and then the fronts. Each side is allowed to dry for 72 hours. Again, the benefit of this process is that it yields very delicate lines with precise detail (i.e., more so than the initial offset printing work). The benefit of the “dry” part of the dry intaglio printing is that the custom printing paper does not expand and contract as it would when wet (or when drying), so there can be more precision in the positioning of the text and images (and more currency bills printed on each press sheet).
To quote from “How Paper Money Is Made,” by www.Littletoncoin.com, “All US paper money features green ink on the backs, while the faces use black ink, color-shifting ink in the lower right corner of $10-$100 notes, and metallic ink for the freedom icons on $10, $20, and $50 bills. The ‘bell in the inkwell’ freedom icon on $100 notes uses color-shifting ink.”
Inspection
Then after all printing (both sides) and adequate drying time comes inspection, using the Bureau of Engraving and Printing Upgraded Offline Currency Inspection System (UOCIS). This equipment “integrates computers, cameras, and sophisticated software to thoroughly analyze and evaluate untrimmed printed sheets” (“How Paper Money Is Made,” by www.Littletoncoin.com). In 3/10 of a second the software accepts or rejects the sheets based on ink density and color register. Then it trims the 32-up sheets into two 16-up sheets.
Additional Printing
“COPE-Pak adds the two serial numbers, black Federal Reserve seal, green Treasury seal, and Federal Reserve identification numbers” (“How Paper Money Is Made,” by www.Littletoncoin.com). During this process, the COPE Vision Inspection System (CVIS) checks the sheets for accuracy and either passes them or rejects them, replacing the rejected sheets “with a ‘star sheet.’ Serial numbers of notes on star sheets are identical to the notes they replaced, except that the star appears after the serial number in place of the suffix number” (“How Paper Money Is Made,” by www.Littletoncoin.com).
Trimming and Packaging
Finally the 16-note sheets are cut down into individual bills using guillotine cutters. These individual bills are shrink wrapped in stacks of 4,000 notes and then transferred to the Federal Reserve.
The Takeaway
Here are some thoughts:
- Printing money is an education in itself regarding the use of multiple commercial printing techniques on a single job, with the best technology used for each element of the overall process.
- Using color-shifting ink, special strips, watermarks, etc., the Bureau of Engraving and Printing minimizes the chance of counterfeiting. These are extraordinarily sophisticated devices. Keep in mind that printing paper money is actually an example of “functional” or “industrial” commercial printing, since the goal is utilitarian rather than informative or promotional. The overall design has to work. That is, it must carry financial value (intrinsically, in each note) while making it hard if not impossible for others to duplicate. To these ends, currency designers employ special inks and special papers (that have to be tightly tracked) with watermarks, security threads, and interwoven strips.
- Moreover, since it is an example of functional commercial printing, the process of printing paper money needs to ensure the durability of these notes as they change hands (i.e., accounting for bodily oils from the hands, folding the bills, and the bills’ rubbing against other items in wallets). So the length of time the bills can be used is a testament to the durability of the 75 percent cotton/25 percent linen mix of the currency paper fibers.