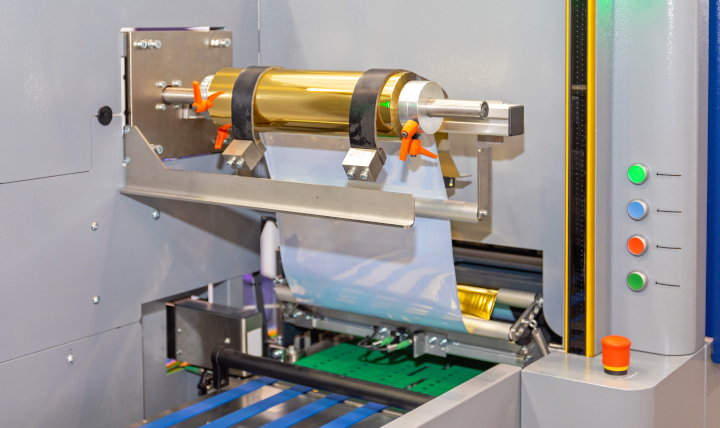
Photo purchased from … www.depositphotos.com
It’s easy to forget that commercial printing is more than just a process of putting ink or toner on paper, and miss out on all the other operations that contribute to the overall success of a custom printing job.
A lot of these processes follow the printing step and are therefore referred to as post-press operations or finishing operations. Strictly speaking, even folding and trimming the stack of press sheets after the ink has dried would fit into this category, but today we will focus on three post-printing techniques that give dimension to a printed product: die cutting, embossing/debossing, and foil stamping.
Above all else, commercial printing is a tactile medium. You become especially aware of this when you compare a 256-page perfect-bound print book with French flaps to the same book presented as a file on an e-reader. The print book has heft. The text and cover papers have a rough or smooth feel. And there’s usually a scent associated with a printed paper product.
The three post-press operations I have mentioned add to this tactile nature and accentuate the dimensionality of the printed piece (which is, above all else, a three-dimensional object).
Die Cutting
Die cutting is done on a letterpress. That is, it is a physical stamping process, unlike offset printing, which depends on a chemical property: the immiscibility of oil and water. (Oily ink and water do not mix.)
A letterpress performs a physical, relief-printing process (the image areas are raised above the non-image areas). In the case of die cutting, flexible metal rules are bent into the shape required (let’s say a square to be cut out of the front cover of a presentation folder). These rules are set into a wood base with the edge of the cutting rules raised above everything else. When the letterpress is operated with the presentation cover paper in place, the die rules will chop through the paper. Then the scrap (the portion to be removed) can be discarded by the press operator.
(A similar process can be done for scoring, which is the creasing of thick custom printing paper to allow for smooth, even folding. It can also be done for perforating, which uses a metal rule to punch a row of tiny holes in commercial printing paper so it can be torn smoothly by the end user. While these are also done on a letterpress, they can in some cases be done on an offset press, with the metal scoring or perforating rules attached to the impression cylinder of the offset press. Unfortunately, this eventually destroys the rubber blanket on that particular unit of the offset press.)
Die cutting is used extensively in product packaging. If, for example, you take apart a carton of tea bags from the grocery store (to the point at which all glued portions have been separated and laid flat), you will see that it is composed of an irregular form with a number of flaps. (The same is true if you take apart a presentation pocket folder.) The metal die cutting rules punch out this intricate shape, which when folded and glued yields a rectangular product box.
Dies are always an extra cost. In my experience they often cost between $250 and $500. That said, every time you reprint a job using the same die, you already have it on hand and don’t need to pay for a new die. You just have to pay for the die-cutting process. In addition, for standard dies that many customers might use, your printer may already have these on hand, so you may not need to pay for and wait for a new one.
Embossing/Debossing
Also using a metal die (in this case a two-part die), you can use a letterpress to raise or lower an image above or below the rest of the printing sheet (up to about 1/8”). You would do this after the custom printing component of the job. Otherwise, the pressure of the offset printing press would crush the sculpted image.
In embossing and debossing, one part of the two-part die pushes the design into the paper fibers, while the other part of the die receives this impression, allowing the paper to move forward or backward in accord with the image. This is done with heat as well as pressure to allow the paper to be sculpted more easily, and this adds a smooth surface to the embossed or debossed area as well.
Embossing and debossing dies (embossing raises the image above the rest of the paper, while debossing lowers the image) can be quite intricate, and the edges of various parts of the die can even be at different levels of depth. However, if the lines are too fine, they may cut through the paper (that is, the goal is to form the paper without cutting it).
In addition, if the dies are especially deep, they may need to be beveled (staggered in multiple layers) to avoid cutting into the paper, and this can make the image area of the embossing/debossing look smaller than it actually is.
So involve your printer early in the design process to ensure that your design will work on a physical as well as aesthetic level.
In some cases, you may choose registered embossing, in which the raising or lowering of the paper surface is in register with a previously inked image. This may also be the case if you’re foil stamping a job. For instance, you may want to register a foil seal and an embossing stamp for an award symbol on a certificate or book jacket cover, or even the words in the title of a print book on the book’s dust jacket.
If you just want to emboss or deboss a design on paper without registering it to previously printed ink or previously foil-stamped images, this is called blind embossing. In this case the three-dimensional raised or lowered effect is the complete design, without any printing.
Such soft “text papers” (i.e., high-end textured papers) as felt stock are good for embossing/debossing because they are thick, durable, and soft. This helps them take the impression of the metal dies better than a harder press sheet.
As with die cutting, embossing/debossing will require extra time (dies are subcontracted out by your printer) and will add to the cost of the custom printing process.
Foil Stamping
Another strike-on process used to embellish your print book dust jacket or even the cloth of the case binding itself is foil stamping. This is also good for the starburst seals on certificates of appreciation. In either case a metal die is created with the image area of the artwork slightly raised.
This die is then heated and pressed against a roll of thin foil, and the heat and pressure attach the foil to the substrate. The fabric of book covers actually accepts this process quite readily. In the case of certificates with raised foil seals, the foil-stamped certificates can then be embossed as described above.
Interestingly enough, this process can also be used for physical products such as pencils, pens, frames, and such.
In addition, you have a much wider range of choices of foil than you might think, including metallics, pastels, patterns, and even clear foils and foils that match the background (such as gloss or dull black to be attached to black paper). So in this way you can create contrast between the text and background.
Foil stamping is great for rendering text on dark paper, for instance an invitation with white lettering on a black background. Since offset inks are transparent, it would take two or three passes with ink to create a completely opaque image, whereas the foil is already opaque, so all you need is one pass through the press.
The best paper to foil stamp is either a textured stock (a premium “text” sheet) or even a high quality bond paper.
Granted, as with die cutting and embossing/debossing, foil stamping requires the cost and time involved in cutting (chemically or by hand) a metal die.
Getting It Printed, a text on commercial printing technology by Mark Beach and Eric Kenly, notes that foil can blister if applied over inks containing silicone or wax, or even over coated paper. In addition, applying foil over too large an area (more than eight square inches) may also cause blistering.
On the plus side, Getting It Printed mentions that these plastic foils can stretch, which makes for a successful pairing of embossing and foil stamping.