Printing Industry Exchange (printindustry.com) is pleased to have Steven Waxman writing and managing the Printing Industry Blog. As a printing consultant, Steven teaches corporations how to save money buying printing, brokers printing services, and teaches prepress techniques. Steven has been in the printing industry for thirty-three years working as a writer, editor, print buyer, photographer, graphic designer, art director, and production manager.
Need a Printing Quote from multiple printers? click here.
Are you a Printing Company interested in joining our service? click here. |
The Printing Industry Exchange (PIE) staff are experienced individuals within the printing industry that are dedicated to helping and maintaining a high standard of ethics in this business. We are a privately owned company with principals in the business having a combined total of 103 years experience in the printing industry.
PIE's staff is here to help the print buyer find competitive pricing and the right printer to do their job, and also to help the printing companies increase their revenues by providing numerous leads they can quote on and potentially get new business.
This is a free service to the print buyer. All you do is find the appropriate bid request form, fill it out, and it is emailed out to the printing companies who do that type of printing work. The printers best qualified to do your job, will email you pricing and if you decide to print your job through one of these print vendors, you contact them directly.
We have kept the PIE system simple -- we get a monthly fee from the commercial printers who belong to our service. Once the bid request is submitted, all interactions are between the print buyers and the printers.
We are here to help, you can contact us by email at info@printindustry.com.
|
|
Archive for the ‘PrintBuying’ Category
Tuesday, October 24th, 2023
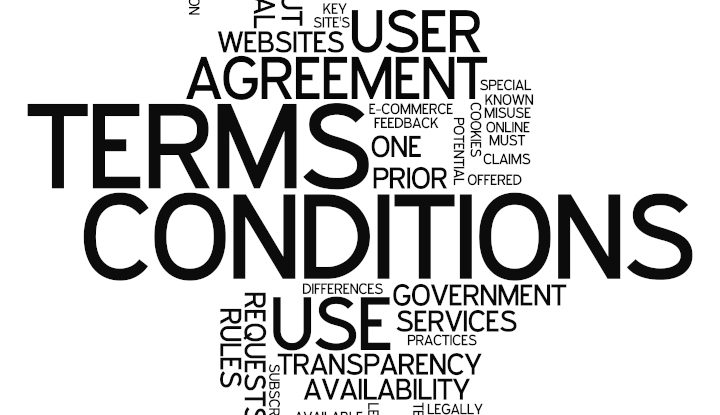
Photo purchased from … www.depositphotos.com
The Printing Industry Exchange Blog is #12 of the best 40 digital printing blogs, as selected by FEEDSPOT.
A relationship with a printer is just that, a relationship. To move forward, it must involve mutual trust. You need to know the printer will produce your job in a satisfactory way, and your printer needs to know you will pay as agreed.
This PIE Blog posting is a case study about agreements and expectations, and how there can unfortunately be a perfect storm when everything goes wrong. At the same time, there are ways to minimize this chance, and to understand the spoken and unspoken agreements with your commercial printing vendor based on accepted industry standards.
The Backstory
I am currently addressing a payment situation with a client for an annual report promotional mailing.
This is the job: a 24-page annual report in 4-color process ink, trimmed and saddle stitched; a 4-color letter on 60# offset stock; a 28# open-side envelope (which opens on the long side and is therefore “machinable,” which means it can be stuffed on a machine rather than by hand); and all mailshop work to prepare 1,500 copies of the aforementioned package and enter them into the mail stream.
All of this was produced over the course of the summer, which is prime vacation time for both commercial printing vendors and my clients–which led to people not being present to read and sign contracts, cut and sign checks, and respond to emails. Fortunately, the printer had enough staff to keep things going at all times, and I made sincere attempts at all times to contact my client (and/or her boss) in a timely manner with all contracts, schedules, and requests for payment.
The Schedule
The long and short of the matter is that a contract was drafted and signed in late May, and an initial request for half payment was made in early June. The half payment was not made in a timely manner, and at the end of the third week the printer put the job on hold, moved the annual reports, envelopes, and promotional letters into storage, and requested full payment plus estimated postage in order to continue.
(Keep in mind that my client is a “cash” client, not a “credit client.” Therefore it is within industry standard for the printer to require half payment before work starts–to cover the direct cost of buying printing paper, for instance. And it is within industry standard for the custom printing supplier to require final payment before shipping, unless the client has established credit terms. Postage is a direct cost, up-front, paid to the US Postal Service, so it is within industry standard for the printer to request and receive this estimated payment before the mailshop preparation or mail drop: the entry of the product into the mail stream by the Post Office.)
With that in mind, I encouraged my client to pay by electronic funds transfer rather than by check to eliminate any chance of delay in the mail delivery. I also explained in writing the reason the printer now required full payment, rather than half payment, to proceed.
By the end of a week’s time my client’s accountant (outsourced, not in-house) had sent out two checks (half payment and full payment) in error—and without using the faster option of the electronic transfer of funds. The process would have gone more quickly if two of the three participants had not been on their summer vacations.
I asked the printer to let me know when the checks had arrived, to destroy the check for the lesser amount, and to let me know when the remaining check had cleared (and therefore when work on the job could resume).
The job went into the mail as soon as it could. Unfortunately, this occurred about two days after the US Post Office raised postage rates, incurring just under $400 of additional charges for my client.
Needless to say, my client refused to pay the surcharge and said the printer was responsible because they had held up the job. This is where things are now.
What You Can Learn to Avoid This
All of this was the perfect storm of miscommunication augmented by key people being out of range of communication (due to summer vacations). I have drafted a letter to my client including a timeline of all activities, from the signing of the contract through billing, and including all invoices from the printer and the US Postal receipt (Form-3600R) for the mailing.
I have not heard back yet, but the bottom line is that since I had kept all relevant emails describing what was agreed upon and what had happened (plus references to the standard printing industry terms and conditions), I expect an eventual positive resolution. We’ll see what happens.
That said, this might happen to you (maybe once in your career as a designer or print buyer), so you may want to consider the following to help you sidestep such a nuisance:
- First of all, postage estimates from the printer are just that—estimates. The printer will bill you for additional costs or refund to you any credits you are owed.
- You can pay by cash, credit, or Visa in many cases. Payment by Visa will probably incur a 3 percent surcharge. “Cash” terms will require a down payment and a final payment before the job can be delivered to you or mailed to your clients.
- I particularly like the option of electronic funds transfer for payment. Funds go from your company’s bank to the commercial printing vendor’s bank without any chance of delay or loss in the mail. The transaction (and the clearing of funds) will go much faster than the check writing, mailing, and bank-clearing process. In most cases this service is offered for free and sidesteps the 3 percent credit card fee.
- You may not want to establish credit terms. Not that your credit is bad, but I believe an inquiry may affect your credit score. That said, if this is not a concern for you, you may appreciate being billed and having 30 days to pay.
- Your custom printing supplier has to charge you up front because he must buy paper, and this is a major expense. He can’t be expected to front the money for paper, or for postage for that matter.
- Charging you before releasing your job ensures your full payment in a timely manner. After all, the printer can’t front all monies and then come to you for reimbursement.
- Schedules are important. Printers take holidays, too, and count workdays as Monday through Friday only, not Saturdays and Sundays. If you need rush services, this may be negotiable for a higher cost (i.e., to hire more staff to complete your job more quickly).
- Good planning and communication with your printer are essential. If a company’s accounting services are outsourced (which is the case with my client), in slow times (such as late summer during vacations) unforeseen delays in payment can occur.
- It’s important to keep records (written notes as well as a history of relevant emails) to explain your workflow should something go wrong.
- No one wants to be considered a difficult client. The preceding list shows the importance of requesting a bill once you have signed the printer’s contract, and then paying it promptly on the agreed-upon schedule. Nothing will better ensure the timely delivery or mailing of your print job.
- It would be wise to read the “Terms and Conditions” page of your printers’ contracts and familiarize yourself with the customs and standards of the commercial printing industry. Getting It Printed by Mark Beach and Eric Kenly is an outstanding book on custom printing, and it includes a copy of these in the text. (This may be out of date, since my personal copy of the book is a number of decades old. So you may want to Google these printing terms and conditions as well.)
The Final Takeaway
If you understand the written and unwritten laws of conducting business in the field of commercial printing, you can see what your rights and responsibilities are as well as what your printer’s rights and responsibilities are. This will keep your response to any problems on a logical rather than emotional level.
I’m sure my client was completely authentic in feeling he had been mistreated by the printer and by the Post Office. That just happens to not be relevant to the agreements made with the printer and the rules pertaining to US Postal Service rate increases.
We’ll see what happens.
Posted in PrintBuying, Printing Contracts | Comments Off on Custom Printing: Case Study on Scheduling and Payment Terms
Sunday, May 14th, 2023
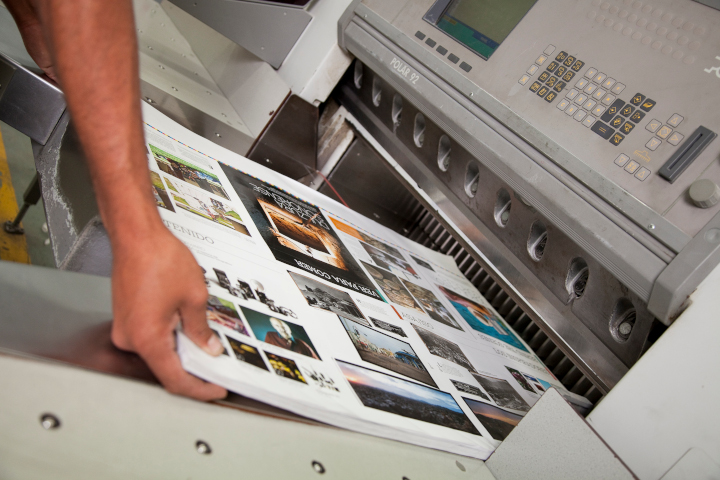
Photo purchased from … www.depositphotos.com
Some commercial printing jobs go south. It’s a fact of life. Here are some lessons you might want to consider based on issues I just had with two of my recent print jobs.
That said, it’s actually helpful to approach things in the following manner. Fixing a problem job for a client who is disgruntled, as well as learning something of value for future jobs, makes you a better print buyer than having all jobs run without a hitch.
The Husband-and-Wife Publishing Team
I recently reprinted a 6” x 9” perfect bound literary print book (i.e., with high production values needed to compete with digital books sold at a lower cost) for a husband-and-wife publishing team. I have worked with this client for over ten years. The two principals of the small publisher love the physical nature of the print book, and they share this love with their literary clientele.
Unfortunately, in this case there were three problems.
The first had to do with folds that were slightly off on the French flaps (3.5” extensions to the front and back cover, folded over the front and back inside covers to give the impression that the book has a dust jacket). These also provide room for additional promotional information. Unfortunately, some of these were not absolutely square (or true).
In addition, the color on some of the book covers was not as saturated or intense as on the original printing of this book.
Finally, in spite of my client’s explicit delivery instructions, all copies of the print book came to her and her husband’s house. They should have received 50 samples. Instead, they received 750 books, 700 of which needed to be at the print book distributor’s warehouse halfway across the country.
Needless to say, I asked my clients to check multiple copies of the books from multiple cartons to determine the extent of the color problem and folding problem, but I addressed the shipping problem immediately because their unsold books needed to be at the book distributor yesterday if not sooner.
Fortunately I had the exact email in which my client had set forth her delivery needs, as well as proof that she had sent this email directly to the printer. With this in hand it was easy to get the book printer to provide appropriate labels for the ten boxes of perfect-bound books to facilitate UPS’s picking them up and re-delivering them immediately.
My client was happy with the speedy service. Having the books picked up and rerouted went a long way.
Furthermore, the printer’s rep for this book offered my client a discount on the problematic books with folding issues and color intensity issues. She hadn’t been asked for this discount. She offered it on her own. My client was especially touched and felt well taken care of in spite of the custom printing issues. At the moment, while her books are being rerouted to the book distributor, my client is tallying up the number of less than perfect books, which already seems to be a smaller number than initially expected.
Moreover, I asked my client to compare the printed book covers to the contract proof she had received from the printer. (The printer had produced two copies: one for their use and one for hers, so my client still had a copy of the cover proof.) Apparently the proof, which my client had initially told me she had liked, did match the final books she had received.
So as the book printer’s speedy attention to making my client and her husband happy moved forward, the scope of the problems gradually decreased.
What We Can Learn
When things go wrong with shipping, which does happen, it always helps to have the email in which you specifically stated what printed copies had to go to which destination point. In fact, it may help to make sure this information is also noted on the printer’s proof sign-off sheet, or to confirm in some other way this information before the cartons ship out. If anything changes, then update the delivery spec sheet and send it to the book printer noting explicitly that it is an update to the original information.
Regarding my client’s color issues and folding issues, I had made an initial assumption that might not have been adequate. I had assumed the art files had been correct for the reprint. What I should have also done is ask my client to send a sample from the initial printing of the book for the printer to match. A physical copy when compared to the ink density and folding issues would have shown exactly what my client wanted. Sometimes the printer’s physical proof and the original art files are not enough (particularly when you’re trying to match a prior press run).
The Fashionista’s Color Chin Cards
I mentioned this job in several past issues of the PIE Blog. My client is producing a set of laminated chin cards. These cards (with a series of full-bleed solid ink hues showing what fabric colors and makeup will be complementary to one’s complexion when held under one’s chin) are 8.5” x 11”, laminated on both sides, and printed on card stock.
I had expressed concern that if produced on a laser printer these cards might have banding problems (uneven lay-down of toner showing streaks through the solid colors). After all, the colors were full bleed, on large cards, with heavy coverage of the colored toner particles. Foreseeing any problems with such banding was my goal in suggesting my client purchase an initial complete set as a proof. Unfortunately, I was right. (I’m usually much happier when I’m wrong.) There was banding. So my client gave the job to another printer.
Rather than lose a client entirely (since she also produces much smaller color swatch books based on the same color system), I thought ahead.
I thought about the HP Indigo color laser printer, which uses much smaller toner particles suspended in fuser oil (rather than the much larger dry color toner particles used in many other digital laser presses). I thought this might minimize banding. I realized this flaw occurs in many cases where the color is built up with multiple layers of cyan, magenta, yellow, and black toner particles, and thought it would be more evident in a large space, like an 8.5” x 11” full-bleed chin card. But I thought the HP Indigo process might be more forgiving.
That said, I also thought back to the three times this job had been printed without incident, without banding. The printer I had used had actually brokered out this digital job himself. I happened to know the kind of press he had used (a Fujifilm J Press, a production inkjet press, rather than the HP Indigo, the color laser digital press I was considering).
I thought a bit further and spoke with a printer who has this digital press. Apparently, since it is an inkjet press, it builds color with minuscule dots (more or less of the cyan, magenta, yellow, or black ink just means more or fewer minuscule dots). This was the technology used for the prior three printings of the chin cards without any visible banding.
At this point, although I know that even inkjet print heads clog from time to time and yield poor quality printing work, I still thought this might be a future option to win back this job. Granted, it will require my client’s seeing samples from this J Press and probably also paying for a full-size, complete proof of all the color chin cards. Since this job is reprinted at least once a year, it doesn’t hurt to have a new printer in the wings who can potentially produce quality work, with consistent color and no banding, for each reprint.
What We Can Learn
Never give up. Actually, that’s the gist of the lecture I received from my fiancee.
My own suggestions have to do with research and being open to multiple technologies. My client’s job was too small (too short a press run, 50 sets of 72 pages, back and front, or 36 leaves) for offset lithography. The only option was digital. That said, there was traditional dry toner (the toner particles don’t always land as precisely as offset ink). There was HP Indigo’s minuscule toner particles suspended in fuser oil. And there was production inkjet, with colors built from process inks using minuscule stochastic spots rather than much larger halftone dots.
At least this is my current assessment, my hypothesis. But I do have to see this hypothesis confirmed with printer’s samples and a physical proof.
I urge you to take the same approach with the commercial printing jobs you buy.
Posted in PrintBuying, Printing | Comments Off on Custom Printing: What to Do When a Job Goes South, Chapter 2
Saturday, May 6th, 2023
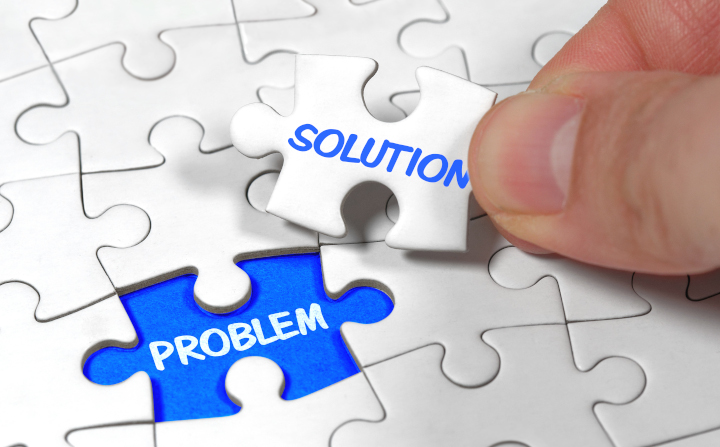
Photo purchased from … www.depositphotos.com
A good working relationship with a printer is like a marriage. It takes work. It also doesn’t always go the way you want it to. Sometimes a job goes south. This doesn’t mean it’s time to get up and leave. It just means you need to find a solution that works for both you and the printer. I think most people would not necessarily acknowledge this, since it’s human nature to be angry and get into blame when something goes wrong.
Examples
I used to be a lot harsher, back in the ‘90s when I was an art director and production manager at a government education nonprofit foundation. I remember sending back a delivery of stationery in which the two colors of the logo were out of register. I told the first printer I didn’t want to see a bill, and I sent the job to another printer. Maybe this was, in fact, the right approach. After all, this stationery was for the CEO of the company.
Another time, I sent back a job in which a photo had been flopped (printed backwards). This didn’t show up in the blueline proof (we didn’t yet scan our own photos). The image had been “right reading,” but in the final print job it was “wrong reading.” The photo included the company’s logo pictured prominently (and backwards). I asked for this job, a newsletter, to be reprinted. Now that I think of it, maybe this was the right approach.
Unfortunately, we started to get a reputation among the printers we used (I and the three designers who worked for me). Some printers were hesitant to work with us.
I was slightly more than half my current age. I’ve mellowed a bit since then. Now I prefer a mutually agreeable solution.
How Bad Is Bad?
About 15 years ago I brokered a book printing job for (as I recall) the Embassy of Chile in Washington, DC. The problem was that all the pages in all of the print books were wavy (as opposed to completely flat). My client at the embassy had followed my suggestion and had checked random samples within all of the cartons of books. So there was a reasonable expectation that the problem was pervasive.
This time, instead of sending everything back, I called the printer and asked for suggestions. He said I should turn the cartons of books over (to change how the books lay in the cartons in order to adjust their weight distribution) and then wait. Within a week’s time they had flattened out. The pages were no longer rippled or wavy. My client was very happy and more than a little impressed (as was I by the book printer’s ability to solve the problem).
(My guess at this point was that the covers had been printed via sheetfed offset lithography and the text blocks of the books had been printed via heatset web offset lithography. The books were probably bound and trimmed without letting the text blocks absorb ambient moisture after traveling through the heating units of the web press and then being cooled abruptly by the chill rollers.)
The reason for the problem was actually less relevant than the fact that the book printer solved my client’s problem. Moreover, the print books (while not great when they had wavy pages) were still usable for initial distribution (of a few copies), and as soon as the waviness had relaxed, everything was good to go.
But what if the waviness had never gone away?
How bad is bad? This was fixable. Another project was not. The covers of the print book I brokered for another client were “painted” (heavy coverage of a solid color) with full-bleed black ink from which the cover photo was knocked out. It was rather dramatic.
Unfortunately, the book-cover lamination was added before the ink was completely dry. The slightly wet cover ink gassed out (gave off a gas), which produced bubbles that lifted the lay-flat laminate off the press stock. Again, it was bad in different ways, but for the most part it affected all copies.
So I had the book printer take off the covers and reprint them, wait longer this time for the ink to dry, and then rebind and retrim the print book. Unfortunately the trim size was then slightly smaller than originally intended. In itself, this could have caused horrible design problems. Design elements could have been too close to the trim and been chopped off (or, on an intuitive level, they could have felt like they were too close to the trim). I myself had actually designed the book and had left adequate margins, so everything was good.
The printer was not happy, but he wanted my future business (this is why it’s good to nurture mutually-advantageous commercial printing relationships with your vendors). He also had to trim every book by hand one at a time (not really by hand, since he did use mechanical trimming equipment, but it was a slow and arduous process).
In this case the printer’s cost in lost revenue was less than the cost to reprint the entire book. My client would have accepted nothing less (and certainly not just a discount). Why? Because she was selling the print book and it was ugly (i.e., unusable and unsalable) until the problem had been remedied.
Another client regularly reprints her (approximately) 2” x 3” color swatch books, which people use to choose colors for makeup and clothing that complement their complexions. I forgot to adequately explain to the printer how the job was to be laminated. In haste I made a mistake. So I paid out of my pocket to have the job reprinted.
In this case it was not the printer’s problem. It was mine, as my client’s broker. Unlaminated cards would not have been salable (would not have suited my client’s needs). The problem was pervasive (it affected all color swatch books). There was no other answer but to reprint.
What to Do
Boom. The job arrives. Look at it immediately. With a critical eye. Don’t put this off. You haven’t accepted delivery of the job until you have checked it and responded to the printer. That’s how I’ve always looked at this process.
If there are problems, alert the printer immediately and start to check random samples in a number of the cartons to get a good sense of the extent of the problem. You don’t have to check every item. You will start to see patterns. For instance, maybe the problem is only in samples taken from one carton. Maybe the color shifted in a handful of press sheets, and the pressman didn’t catch the error.
Then document everything with photos and a written description of the problem and its extent.
For instance, recently the client with the color swatch books had color shifts in her finished books. She did what I just suggested and told me the problem was evident in 10 books out of 200. Five percent. They were usable. One client complained.
We settled on free shipping for the next reprint plus an agreement to use a different digital press and a more robust sample-press-sheet checking process. My client was happy (above all else, this is the goal). How did we arrive at the amount? Ten books at I believe about $15 each (total cost of the job divided by 200 books). A fair trade: the shipping cost for free.
I had another issue once with a printer in Canada. He was producing a magazine regularly for one of my clients. As I recall, he had to reprint a press signature of the magazine for some reason. We agreed to “split the difference,” to share the cost of the extra press run. Without my remembering the details (it was 23 years ago), I do remember that in this case the reprint was necessary and not clearly the printer’s fault, so the resolution was fair. Both parties (the printer and my client) were not happy but also didn’t feel taken advantage of. My client printed the magazine at this vendor’s shop for many issues going forward.
(In your own work, another approach might be to ask the vendor about reprinting the job at his actual cost rather than at your normal cost including the printer’s mark-up.)
Overall, this is a judgment call. Do the research into the problem, its cause, and its extent. Then decide what will make you whole. Can you accept the job at a discount? Or do you need a reprint?
Overall, the goal is to get a satisfactory printed product and also to be able to continue one’s long-standing, mutually beneficial working relationship with the commercial printing vendor. This depends in large part on the lines of communication and mutual trust you have nurtured over a number of custom printing jobs.
A printer friend of mine calls a job printed for a client who has never printed with the company before, who probably chose the printer based solely on price, and who is not likely to work with the printer again a “drive by.” This is what you don’t want to be and understandably so. It actually benefits you as well as the printer–over your time working together on multiple print jobs–if both you and the printer “win” rather than if one of you loses.
That’s why I say it’s like a marriage.
Posted in PrintBuying | Comments Off on Custom Printing: What to Do When a Job Goes South
Sunday, March 19th, 2023
Photo purchased from … www.depositphotos.com
A long-term, mutually beneficial business relationship with a printer sometimes ends. Perhaps the printer goes out of business or starts to not be as responsive as in prior years. Maybe their prices even rise dramatically, making the company no longer an option. What can you do?
In this light I have a case study to share. One of my commercial printing clients produces a color swatch book on a regular basis. These tiny, screw-and-post books are like PMS swatch books for those looking for make-up and clothing colors that will complement their complexion and hair color.
Along with this set of color swatch books, my client prints larger chin cards with a die cut for the person’s neck. These 8.5” x 11” chin cards allow the user to hold a large color swatch under her chin to see how a particular hue will look with her skin tone and hair color.
The cards are 8.5” x 11”, 14 pt. in thickness, with a semi-circle die cut for the chin, and with lamination on both sides. One side of each card is a big swatch of color bleeding on all four sides. The other side is text in black ink only. The total set comprises 72 pages (35 colors with information on the back of each, plus one single-page (front and back) set of instructions.
Losing a Printer
My color-swatch-book and chin-card client recently lost her printer based on issues with management. This particular printer had produced 50 sets of her chin cards every other year or so. The colors had been faithful to her expectations, and there had been no banding or artifacts in the solid, digitally printed colors, so it had become an easy reprint on a periodic basis. A boon to the printer (it was regular, straightforward work) and to my client (the end result was predictable).
So losing the commercial printing vendor was unfortunate. I had actually gone through a similar loss of a printer for my client’s color swatch books for a different reason several years prior. This vendor had upgraded the software on their HP Indigo digital laser press, and for whatever reason a number of the colors of the (smaller than 2” x 3”) swatch books were no longer accurate. This was a harder problem to solve, and it also came down to finding a new printer.
Digital vs. Offset
One of the challenges with replacing the custom printing supplier for the color swatch books (and this will also be true for the color chin cards) was to ensure color accuracy and smooth, even color laydown (compared to offset printed solids). All colors are percentage builds made from the four process colors. There are no PMS colors (since there may be a total of over 100 distinct hues that show up in some of, or in each of, the 28 master copies of the color swatch books).
This would be prohibitively expensive to produce via offset lithography, since it would require multiple passes on an offset press for what would in many cases be only a few copies at a time of the individual swatch books (so many copies of each of the 28 master versions).
For the color chin cards, the same would be true since my client only prints about 50 copies of the 72-page set at a time.
In both cases the limited press run for the individual sets, plus the use of so many colors, requires an accurate and consistent digital press. In my mind that includes the HP Indigo plus perhaps a Konica Minolta plus a Kodak NexPress, although I’m sure in the last several years other vendors have stepped in with equally accurate color digital printers.
With the loss of the color swatch book vendor, and in the most recent case the loss of the color chin card vendor, selecting a replacement has been and will be dependent on a physical proof of all pages.
So I have requested pricing for (in the case of the chin cards, since it’s the current job needing custom printing vendor replacement) a full hard-copy proof from the digital press in question, whether it is a digital laser press or a digital inkjet press (depending on the new vendor).
The color proof will ensure that the color builds (percentages of cyan, magenta, yellow, and black) that my client had specified in her art file (she had kept a digital copy of her chin cards from the prior print run) match her expectations.
This is not always the case for all colors for all commercial printing vendors using a variety of digital presses. And soft proofs (PDFs on screen) of the color swatches (2” x 3” color swatches or 8.5” x 11” color chin cards) would not necessarily present the colors as they will eventually look when actually printed. After all, in the case of a computer monitor proof, the colors are created with red, green, and blue phosphors, whereas on a proof made on the actual press, the colors will have been created from the actual cyan, magenta, yellow, and black toners or inkjet inks.
In my client’s case the die cut and the lamination will be irrelevant, and not including these elements on the printer’s proof will keep the price down ($75.00, approximately, from two of the vendors I’ve approached). I think the cost of such a proof (rolled into the total manufacturing cost by some printers) is an investment, not an expense.
Banding and Artifacts
In my experience, some digital presses also produce solids (in this case up to 8.5” x 11” for the chin cards) that may not be as even a laydown of pigment as with oil-based, thick, offset-printed ink.
Sometimes there are artifacts (stray marks or lines) or banding (usually but not always in gradations from a light tint to a darker shade of a color). I’m not sure whether the banding is a reflection on the number of steps in the gradation (not an issue in the case of my client’s chin cards) or the PostScript (page description language) code of my client’s art file, or even in the nature of the process (spraying ink through nozzles—which sometimes clog) for the inkjet option or using toner particles suspended in fuser oil for the digital laser option.
Regardless, heavy ink coverage can cause problems. And nothing will be as effective in allaying my client’s concerns (and mine) as a hard-copy proof. It will ensure color fidelity (some colors seem to be more problematic than others) and the absence of banding. And once the new printer has proved it can provide an acceptable printed product, my client will have a home for this repeat job for many years going forward.
The Die Issue
Unfortunately, my client will need to have the die for the semi-circular cut out (for the user’s chin) remade. Granted, she paid for it once (approximately $275.00) and it was then used for successive runs of her job. And strictly speaking it is hers (according to commercial printing trade customs). But you could argue that it is only a component of the overall manufacturing process and therefore it belongs to the original printer. Struggling over this for $275.00 may not be worth it.
Availability of Materials
One of the things I’m finding is that not every printer can get the same lamination film for some reason. The job was originally produced on 14 pt. cover stock with 3 mil laminate on both sides of the chin cards. In the cases in which printers have only been able to get 1.2 mil laminate, I have asked for thicker cover stock for the chin card boards.
There is usually a work-around. This is mine.
Other printers may have different approaches. In my case, I think my client will be happy with the printed product as long as the total thickness of the base stock and the laminate on both sides of the cards feels about the same as samples from the prior press runs.
The Takeaway
So there are ways to get around losing a commercial printing supplier, even for a printed product that is a repeat job with colors that may not be easy to match (several of the printers “no-bid” this job outright, concerned that my client would not accept potential color banding or less than perfect colors).
If you have a job like this, it’s worth collecting bids from a number of prospective vendors. The PIE website (I have found) is always a good way to get new printers. Referrals from other clients or other printers that can’t for whatever reason do the job for you would be another option.
But in all cases I feel very strongly that checking an actual, physical proof will put your mind at ease, proving whether the vendor can or cannot provide your required level of quality. Granted, in some cases like these (multiple color builds produced on a digital press), you may need to have some flexibility. Not everything will be 100 percent perfect. Fortunately, my client understands this as long as the hues are reasonably close to the intended color.
But again, all of this will be visible in a good hard-copy proof, and this can help you develop a new long-standing, mutually supportive business relationship with a new printer. It’s a little bit like a marriage. It takes work, but the benefits make it worth it.
Posted in PrintBuying | Comments Off on A Case Study on Replacing a Commercial Printing Supplier
Monday, August 1st, 2022

Photo purchased from … www.depositphotos.com
About twenty years ago I brokered five catalogs to a Canadian printer. I actually found the printer through the Printing Industry Exchange (true story, not a plug for PIE), and I kept the gig going for a number of years. Everything went well. I was pleased. My client was pleased. (more…)
Posted in PrintBuying | Comments Off on Custom Printing: Considering Buying Printing Overseas
Monday, June 27th, 2022
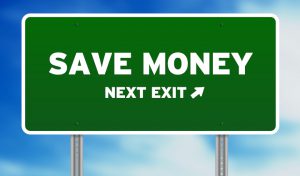
Photo purchased from … www.depositphotos.com
The trick is to realize that most things are negotiable. There are ways to find what you need if you take the time to look. Prices for commercial printing (and especially paper) are going up, but if you’re creative, you can often bring them down at least a bit.
I wrote an initial PIE Blog article on this subject a while ago, so this will be a follow-up article with more tips and tricks for you to consider.
(more…)
Posted in PrintBuying | Comments Off on Custom Printing: More Ways to Save Money When Buying Printing
Friday, April 29th, 2022
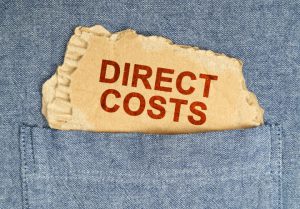
Photo purchased from … www.depositphotos.com
A client of mine recently asked for pricing for her fashion color swatch books: 90 copies vs. 100 copies vs. 115 copies vs. 232 copies. This was to get ballpark pricing. (Her prior run had been 232 copies, so this was the benchmark to which she would compare the other prices.) She planned to open the ordering process to her 4,000 online prospective sales clients and then place the final order through the printer. (more…)
Posted in PrintBuying | 2 Comments »
Monday, October 4th, 2021
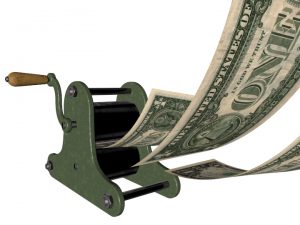
Photo purchased from … www.depositphotos.com
If your job involves either buying commercial printing services or designing print products, your experience over the years will teach you that some custom printing processes cost a lot. It’s easy to spend money quickly on a print job. However, you can also be mindful when designing or specifying a print project and make choices that actually save you money. (more…)
Posted in PrintBuying | 4 Comments »
Sunday, September 12th, 2021
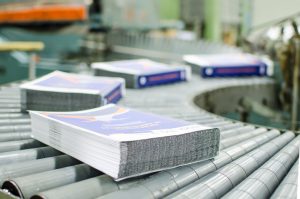
Photo purchased from … www.depositphotos.com
I’ve just received five print book titles to price for two clients. Two of these books have French flaps (the 3.5” flaps that fold in on the front and back cover of a perfect-bound print book, making it look a bit like a case-bound book with a dust jacket). They are a poetry book and a book of fiction respectively, both 5.5” x 8.5” perfect-bound books. One is 272 pages plus cover; one is 72 pages plus cover. Each of these two has a corresponding “reader’s galley,” a book (without French flaps) for 75 selected readers to review and comment on prior to production of the final editions. (more…)
Posted in PrintBuying | Comments Off on Custom Printing: The Current Wild West of Print Buying
Wednesday, August 4th, 2021
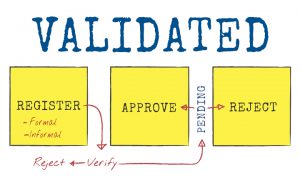
Photo purchased from … www.depositphotos.com
“Acceptable” is a slippery word. In the case of offset and digital printing, acceptable delivery has more to do with whether you can tell your custom printing vendor that you are satisfied with the product and he can bill you for the job. It’s a question of quality, and you have an important decision at this point, which you should not make lightly. (more…)
Posted in PrintBuying | Comments Off on Commercial Printing: Is the Job Your Printer Just Delivered Acceptable?
|
|