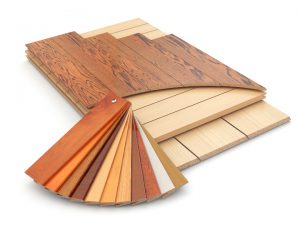
Photo purchased from … www.depositphotos.com
About 30 years ago, when I was an art director and production manager at a nonprofit educational foundation, I worked with a designer and a book printer to reproduce the color and texture of a marbelized, textured paper. This was for an annual report, and the goal was to use a single paper stock for both the marketing portion of the book and the financials. We used a white coated press sheet for everything and printed a photograph of the marbelized paper as a background for all pages of the more elegant marketing section of the annual report. (We also moved the photo around a bit to vary the pattern from page to page.)
This process made an impression on me. I learned that you can make something look other than what it really is by using commercial printing techniques.
About 24 years later my fiancee and I had a house fire. While I didn’t much like the experience, I did learn something about custom printing as we chose materials to rebuild the house. One of these materials was flooring, and I was intrigued by the same process I had seen as an art director. Floor manufacturers were able to use commercial printing techniques to simulate wood grain on various materials and thereby produce flooring sheets and planks that were in many cases more durable and sustainable than real wood but still as attractive.
Initially, I found this somewhat objectionable on a deep level, because I had always been a purist. I always preferred to use real materials and make them look as they really are. Well I got over it. I remember the first time I saw a friend’s composite house-siding shingles. They looked “real,” like wood. But they were concrete, and they could withstand hurricane-force winds. By this time I was also a homeowner—and more frugal and less idealistic than before—and these three experiences came together for me as an “Aha” moment.
Digital Printing and Wood Surface Decoration
Whether it’s real wood with printed patterning or some printed, synthetic base, we are at a crossroads for industrial printing as it applies to the home décor market.
First of all, let’s define some terms and processes. “Industrial printing” is a huge part of commercial printing in general. But it has nothing to do with marketing or education, brochures or books. “Industrial,” or “functional” printing is the utilitarian branch of custom printing. It includes the letters on your computer keyboard keys, the writing on your car’s dashboard, and the numbers on your microwave.
It wasn’t that long ago that industrial or functional printing depended primarily on gravure printing and screen printing. Both of these are labor intensive (i.e., costly) to set up, so for economic press runs, you need to print a huge number of copies. Custom screen printing and gravure also take a long time (for preparation and changeover of jobs), so two things you couldn’t get 20 years ago were immediate turn-around and customization of your simulated wood flooring.
Fortunately for consumers, both of these (speed and variety) have become the norm due to the rise of digital commercial printing, which is ideally suited for “mass customization” and “just in time” manufacturing. So, for instance, instead of needing to order one ton of flooring, a distributor might now be able to order a single, short-run design for one building. This is because of the infinite variability of digital printing.
Another benefit of digital printing addresses the dimensional limitations of the gravure presses that preceded digital technology. The press cylinders had a fixed circumference compared to the laminating presses. Now, on large-format inkjet presses you can produce much wider flooring designs (or designs that don’t repeat regularly).
Better Than Natural Wood
Why do people choose simulated wood products?
-
- They are more sustainable than natural wood.
-
- They may hold up better to the elements.
-
- They may last longer in a damp environment. (After our house fire our water heater developed a leak. The new synthetic basement flooring held up to the flood quite well.)
- They may be more resistant to insects (living in a log cabin is romantic until insects damage the logs).
So digital technologies, whether direct custom printing on wood or lamination, can simulate the color, pattern, and surface texture of real wood, but they can do this on vinyl, metal, or composite wood, in such a way that the floors are more durable, water resistant, and stronger than natural wood. (And having struggled with warped wood in furniture, I personally find that flooring that keeps its dimensional stability even in the bathroom—shower after shower–is a blessing.)
Equipment to Look for and Research
Here are some names of equipment for digitally printed wood decoration that you may want to research if you’re looking into this technology:
- Inca Onset
- Kodak Prosper
- Koenig & Bauer RotaJet
- EFI Cubik
Ask about flatbed inkjet printers that can print directly on thicker substrates (like doors). Ask about roll-fed, aqueous inkjet printers as well. Make sure the printer you choose understands the nuances of woodworking, cabinetry, flooring, and/or lamination. That is, does he understand how digital commercial printing technology for wood surface decoration supplements the more traditional processes?
Moreover, ask about your options. Will your flooring product be directly printed onto solid wood or a flat, thin substrate (lamination)? Will the flooring be impregnated (i.e., what kind of top coating will seal and protect the flooring)?
And here’s a new one to research: Some current flooring decoration technologies will not only print the simulated wood grain on the flooring substrate but will also add a raised surface texture that mirrors the underlying design. (So it not only looks like wood, but it feels like wood, too, and at the same time the flooring product is stronger than natural wood.)
How Can They Ensure the Quality?
Repeatability is of prime importance with flooring decoration. Where two pieces of flooring abut, the colors and patterns must be consistent, or the floor will be ugly.
I have read online recently about “Digital Twin” (cloud-based) technology that ensures the quality of the final product. The gist of this approach is that computers simulate the manufacturing process from beginning to end while monitoring and controlling all steps of the actual, physical manufacturing process. So in most cases they can predict and/or avoid problems. This allows flooring decoration printers to maintain both color and texture consistency while reducing equipment downtime. And the result is higher client satisfaction, increased production efficiency, and increased profitability.
The Takeaway
What can we learn from this new technology? First of all, sometimes you need or want real wood. But sometimes you don’t, and in fact real wood floors might not be as durable or easy to care for as you would like. So there is a real need for wood simulations, particularly since digital technology now provides not only a visual simulation but also a textural simulation. The products look and feel real, and they’re durable.
So if this appeals to you as a designer, take some time to research the options: digital, gravure, custom screen printing. Consider the infinite variability (the opportunities for mass customization) digital printing provides. And think about whether you want to print directly on real, thick wood (doors, for instance) on a flatbed inkjet press, or whether you want to print on roll-to-roll inkjet equipment for follow-up lamination of the flooring product. All of these considerations will lead you to one or more digital commercial printing manufacturers.
And as with all other printed products, ask the suppliers for printed samples. Your eyes and your hands will make the final decision.
This entry was posted
on Monday, April 12th, 2021 at 3:40 pm and is filed under Industrial Printing.
You can follow any responses to this entry through the RSS 2.0 feed.
Both comments and pings are currently closed.