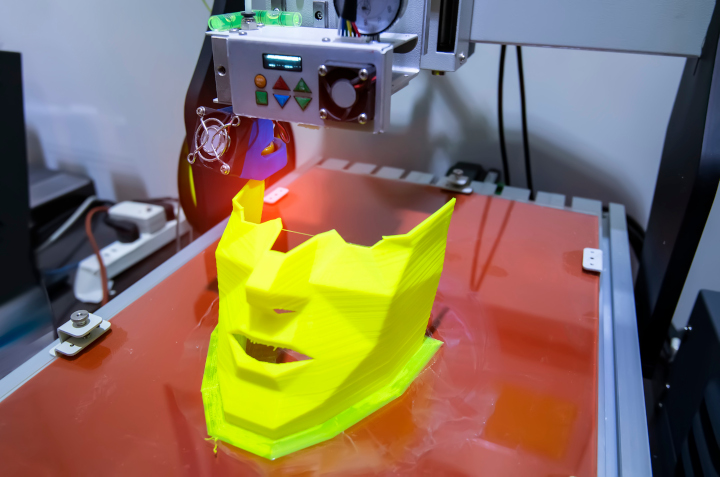
Photo purchased from … www.depositphotos.com
Every day in my Google aggregator email feed, I get a list of digital printing articles and a list of offset printing articles. I find it incredibly useful. In addition to updating me on the technologies and techniques of various aspects of commercial printing, the Google aggregator shows me what’s trending. And recently 3D custom printing has been trending, showing up in a large percentage of the links to commercial printing articles.
In this light, about six months ago I wrote a PIE Blog post about 3D printing. Being a student of offset and digital printing, which in many ways symbolize in two-dimensional form our surrounding 3D world, I’m still finding it challenging to wrap my brain around the concept of making physical “things” with a process analogous to inkjet printing.
You may want to check out Wikipedia when doing your own research, as well as an article I found entitled “What Is 3D Printing?–Simply Explained,” by Lucas Carolo, 02/11/2023, WWW.all3dp.com. Much of what I have written here has been in response to items discussed in these articles.
The 3D Manufacturing Process
Since I don’t have a twelve-year old handy, here’s my 65-year old take, from my cursory research, on what 3D printing is (in non-technical terms) and what implications it has for such issues as copyright protection, reasonable control over firearms, and printing such things as food and medical products (including internal organs).
Plus I will touch briefly on the benefits of 3D printing for the environment, the realignment of manufacturing processes in a world where we can “print our own,” plus challenges for the labor market brought about by the projected growth of 3D printing (or additive manufacturing).
Based on my cursory research, it seems that there are only a handful of steps in 3D printing. First there has to be a computer model, a diagram, if you will, to drive the fabrication of a 3D product. These models can be created with CAD (computer aided design) software packages, or they can even be found online in “repositories.” So you could conceivably just go online, find a computer model for a product, download it, and print it.
The next step is preparing the model for production on your 3D printer. I have seen these in computer stores. They are now very affordable. The ones you or I could buy work with spools of (basically) plastic filament, which are melted and extruded (squeezed out in a stream through a nozzle or print head). This is not unlike an inkjet printer, which does the same thing with liquid ink.
The plastic filament (which looks like a thick plastic wire) builds the physical model layer by layer as the print head travels back and forth over the bed of the 3D printer, which rises or falls as necessary to allow for the growth of the product layer by layer.
Then, the heated plastic solidifies. Or, in some approaches to 3D printing, UV light or even a laser cures the plastic (causes it to harden). For this to work, the computer model must first be “sliced.” Slicing breaks down the 3D computer image into flat layers, which can then be printed one upon the other and thus built up into the final form. This is a mathematical process, as I understand it.
The next step is to print the product. In the case of a desktop 3D printer this process works with different kinds of plastic, but in other additive manufacturing processes 3D products can be made in a similar way with other materials, including metal, ceramic, food, and even biological matter.
To help you visualize this, here’s an analogy. In a nutshell, additive manufacturing is akin to collecting clay and modeling it into a sculpture, while subtractive manufacturing (its opposite) is analogous to chipping away at a block of marble with a chisel to create a sculpture. In the manufacturing arena, subtractive manufacturing would include such processes as “machining” or grinding away metal from an item.
The third option is molding (such as injection molding), which involves pouring a molten material, like plastic or even metal, into a hollow form (the inverse of the final 3D component part) and then removing the mold. This actually can be tied in to 3D printing, because it is possible to either print a mold or print a (plastic) part around which you can then make a mold (for pouring more durable materials than molten plastic).
Most of these processes take time and cost a lot. Among other things, for instance, you would have to create the molds from which you’re making injection molded products (such as plastic toy soldiers).
But with 3D modeling, you just create the computer model yourself, scan a physical object and turn it into a computer model, or acquire the computer model from a repository and then print it.
One benefit of this process is that plastic products made layer by layer from a computer file can be infinitely more detailed than machined component parts. That said, once printed they are usually a bit ragged in areas (or they have supplemental plastic support pieces that hold up the 3D model but that must be removed before use).
So the next step is post processing. (It’s a little like the clean up or finishing work you need to do if you’ve just poured a bronze sculpture into a mold and then opened the mold to find portions that need to be ground away. In 3D printing, you may need to clean up, cure, or paint the pieces, or even assemble them into a larger, more complex final product.
Again, as a reminder, we’re talking about 3D custom printing on desktop machinery using plastic filament, but the concept still holds true for industry-level additive manufacturing.
What’s Is 3D Printing Good For?
The first thing I learned in my research was that companies or individuals could make prototypes easily, quickly, and cheaply.
This is a bit like the prototype a package designer can make before committing to a long run of a particular carton design. If you’re producing a 3D item using subtractive manufacturing or injection molding, you have to build manufacturing equipment specific to producing that particular item.
In contrast, if you’re 3D printing a plastic model head (see the photo at the opening of this article), you can print one copy or ten copies for a small amount of money, quickly. If you’re producing a printed model head as a toy to be sold to children, you can print one, make design changes, and then print a revised version.
This is not true with more mechanical, laborious manufacturing processes (such as injection molding or machining). So your time from idea to prototype to market can be faster with 3D printing, and you have the ability to improve, simplify, or even personalize the 3D plastic head toy each time you print it.
Granted, you can’t print a huge run of these plastic heads quickly or cheaply. This is a more time consuming process for the actual production run (at this point in the development of 3D printing) than the final stage of traditional manufacturing.
Here are some other items that are in vogue for 3D commercial printing at the moment:
- Home décor items such as furniture
- Fashion items such as shoes and jewelry (these can be very intricate, as noted before)
- Firearms
- Food (such as crackers, hamburgers, and even such products as food for astronauts)
- Actual body parts and especially prosthetic limbs. (This doesn’t surprise me, since the medical field has been growing human ears on mice for a long time–on their backs, not their heads.)
- Spare parts that allow people to make their own product repairs at home
3D Printing Is Similar to Inkjet Commercial Printing
As you’re reading this, you may be seeing (as I do) a similarity between inkjet printing in the commercial printing arena and 3D printing with plastic filament in the manufacturing world. You can prototype quickly, personalize your items, print a limited number of copies for a reasonable investment, and easily modify the printout by changing the computer file.
All of this has profound implications, and many of these implications bring to mind the workflow of digital commercial printing.
For instance, since the 3D desktop printers are already affordable, and since they will presumably improve in the near future and use other raw materials such as metals, then 3D printing will presumably democratize manufacturing (make it available to most people, or at least give them more options).
For example, just as you can now write, design, and digitally print publications with equipment that will fit in your home, in the near future you may not need to go to a store to buy something (like a replacement part for a product you own). Instead, you may just download a computer-designed template and print your own replacement part.
Or, manufacturing may move closer to the final destination (think of people who send art files to another state, print their books there, and have a lower freight bill since the printed products are already close to their destination).
Like digital printing, 3D manufacturing will also allow for reduced inventory. Companies won’t need to store inventory since they can 3D print items at the time they are ordered (just like web-to-print for publications). This will save warehousing space and the costs associated with inventorying products, reduce energy for heating and cooling storage facilities, and reduce carbon emissions by minimizing product delivery by truck.
Plus, there will be less material to dump in landfills, since products can be made only when needed (you won’t need to make a huge number of products just because that’s the only way to make the unit costs reasonable). Sounds like digital commercial printing again, doesn’t it?
Social and Ethical Concerns to Address
These are a few of the issues I’ve read about recently:
- Gun control issues. When you can download a template and 3D print your own gun, this can be challenging for the control and licensing of firearms.
- Copyright issues will need to be addressed.
- Ethics issues and religious concerns related to the 3D printing of biological items may need to be addressed.
- Labor issues. The new 3D print workflow will have an impact on labor. Presumably there will be more machines and fewer people getting paid to manufacture items. How will these displaced workers be reintroduced into the labor force?
Welcome to our brand new world.